PRODUCTION
The plant in Rosva Industrial Park is a modern operating plant for the production of full-cycle vehicles, engines, subassemblies and components.
- Production capacity: up to 70,000 vehicles per year
- Suppliers: more than 300 worldwide (85 in Russia, 16 in Kaluga)
- State-of-the-art equipment: ABB, Fanuc, Allen Bradley; Rockwell Automation
- Universal assembly lines
- Flexible robotic welding lines
- Paint shop
- Ability to produce vehicles from class С to heavy body-on-frame SUVs.
- Multi-stage quality control
- Compliance with international quality standards ISO 9001
- Warehouse for final products: 1,800 vehicles
LOGISTICS
The logistics hub in an automotive plant is a key element of the plant infrastructure, enabling more efficient use of available logistics capacities during distribution of inbound and outbound material flows. It plays an important role in optimizing the processes of receiving finished vehicles, components, vehicle production and distribution of final products.
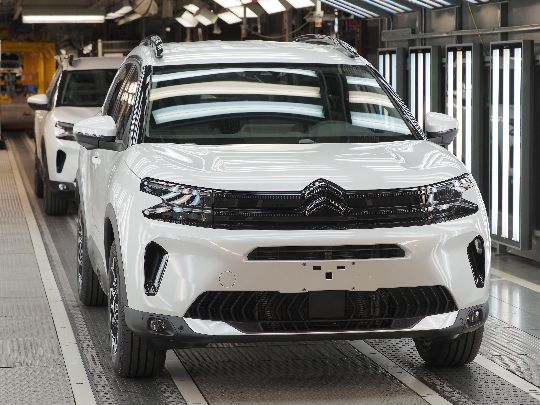
The main functions of a logistics hub in an automotive plant include:
- Inventory management. The logistics hub is responsible for controlling and optimizing the stock of components and materials required for vehicle production. This allows to avoid shortages or overstocking of products in the warehouse.
- Final products delivery. The hub organizes the delivery of final products from the plant to dealers and end customers in direct sales. This includes scheduling of shipments, coordinating with transport companies and managing warehouse operations.
- Process optimization. The logistics hub helps to optimize production processes, reducing the time and cost of delivering components and materials to the points of their utilization. This contributes to improved plant efficiency.
- Accelerated delivery. Thanks to the efficient operation of the logistics hub, the automotive plant's products are delivered faster, increasing customer satisfaction.
The logistics hub is an important tool for improving the efficiency of the automotive plant, making more rational use of available space and the entire infrastructure, as well for ensuring a high level of production.
WELDING SHOP
The welding shop at the “Automotive technologies” plant is a specialised production unit designed to perform welding operations during the assembly of vehicles bodies and other components. It plays an important role in the vehicle manufacturing process, as the quality of welding works determines the robustness and reliability of the vehicle structure and, as a result, its safety.
Various welding methods are used in the welding shop, such as arc welding, contact spot welding, relief welding and others, depending on the requirements for the quality and type of materials to be welded. The welding shop is fitted with modern equipment and tools that ensure high precision and quality of welded seams.
The main functions of the welding shop at an automotive plant include:
The main functions of the welding shop at an automotive plant include:
- manufacturing and assembly of body elements;
- performing welding works in compliance with technological processes and quality standards;
- quality control of welded seams and connections;
- application of sealant and glue using manual and automated devices;
- application of identification number (VIN) on the vehicle body;
- installation of attached parts using screw joints;
- ensuring safety and compliance with labour protection standards.
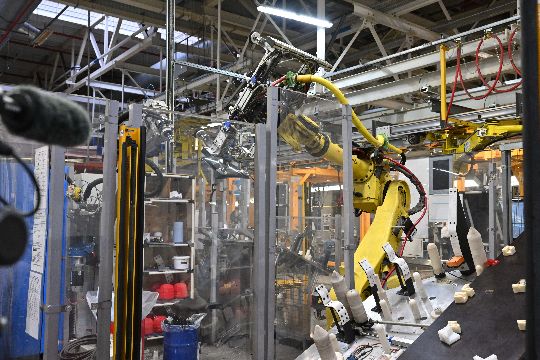
PAINT SHOP
In the paint shop of the “Automotive technologies” plant, paint materials are applied to vehicle bodies or other parts.
The main functions of the paint shop include:
The main functions of the paint shop include:
- surface preparation for painting;
- cataphoresis coating;
- application of paints and varnishes;
- drying and polymerization of the coating.
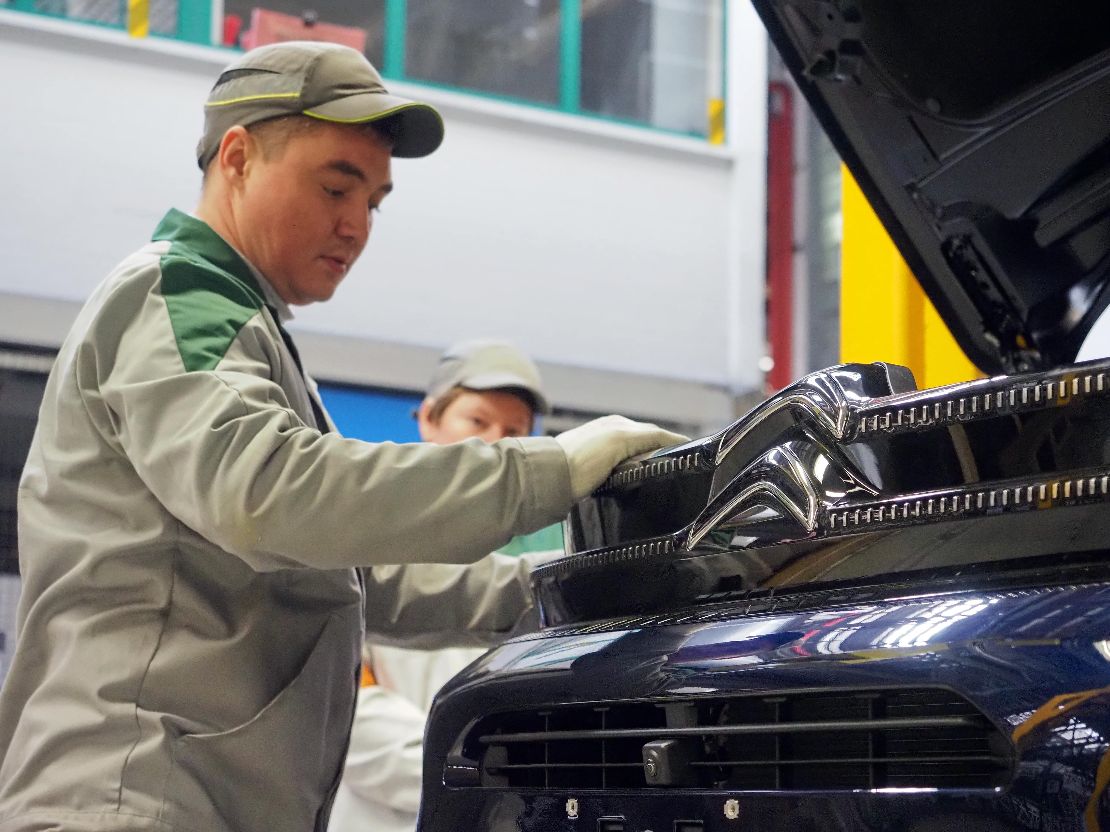
Paint shops are fitted with modern equipment such as paint booths, drying ovens, ventilation and air purification systems. They also have special tools and materials required for painting, such as paint sprayers, compressors, solvents and hardeners, which improve painting quality and labour productivity.
The painting process in the shop includes several stages:
The painting process in the shop includes several stages:
- Surface preparation: cleaning, polishing and degreasing the surface of the body or part. This ensures better adhesion of the paint to the surface.
- Application of a layer of cataphoresis coating to the body in a bathtub with full dipping to increase corrosion resistance.
- Paint application: paint is applied to the surface using robots for the exterior surfaces of the body and a hand-held paint sprayer for the interior. This process requires precision and expertise to ensure even coating
- Drying and polymerization: after the application of cataphoresis and paint coatings, the body or part passes through several drying ovens after each layer, where the solvents evaporate and the coating hardens.
- Quality control: after drying, the paint quality is checked. The uniformity of the coating, absence of defects and colour matching are checked.
ASSEMBLY SHOP
In the assembly shop of the “Automotive technologies” plant, vehicles are assembled from individual components and construction units. This is the stage of production in which all parts are joined into a single whole.
The assembly shop includes the following elements:
- Production lines. In the assembly shop, special lines are organized, on which certain operations are performed to assemble vehicles. These lines are fitted with the necessary equipment and tools to perform the works.
- Conveyors. Conveyors are used to move parts and components from one workplace to another. They help to optimize the assembly process and speed up the production.
- Workstations. The assembly shop is equipped with workstations for specialists who perform the basic operations of joining parts.
- Check points. The shop also has check points where specialists control the quality of assembly and the compliance of the vehicle with technical requirements.
- Storage facilities. Warehouse facilities are provided in the assembly shop for storing parts, components and finished vehicles.
- Production management systems. Assembly shops are equipped with modern production management systems, which allow to automate processes, track the fulfilment of tasks and optimize shop operation.
- Equipment. Special equipment such as programmable torque and angle control wrenches, stations for filling of the vehicles with technical fluids, lifting mechanisms, glass glue robots, tools for mounting and dismounting parts, and quality control systems are used in the assembly shops
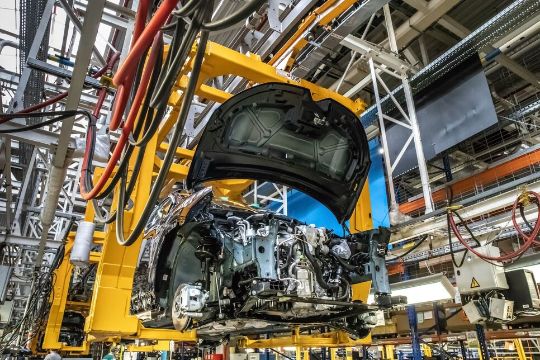
QUALITY
Russian assembly meets the highest quality standards. At all stages of assembly there are quality control stations, where mechanics, electrics, geometry, waterproofing, noise insulation of the vehicle are thoroughly checked and then dynamic tests are performed on a large track.
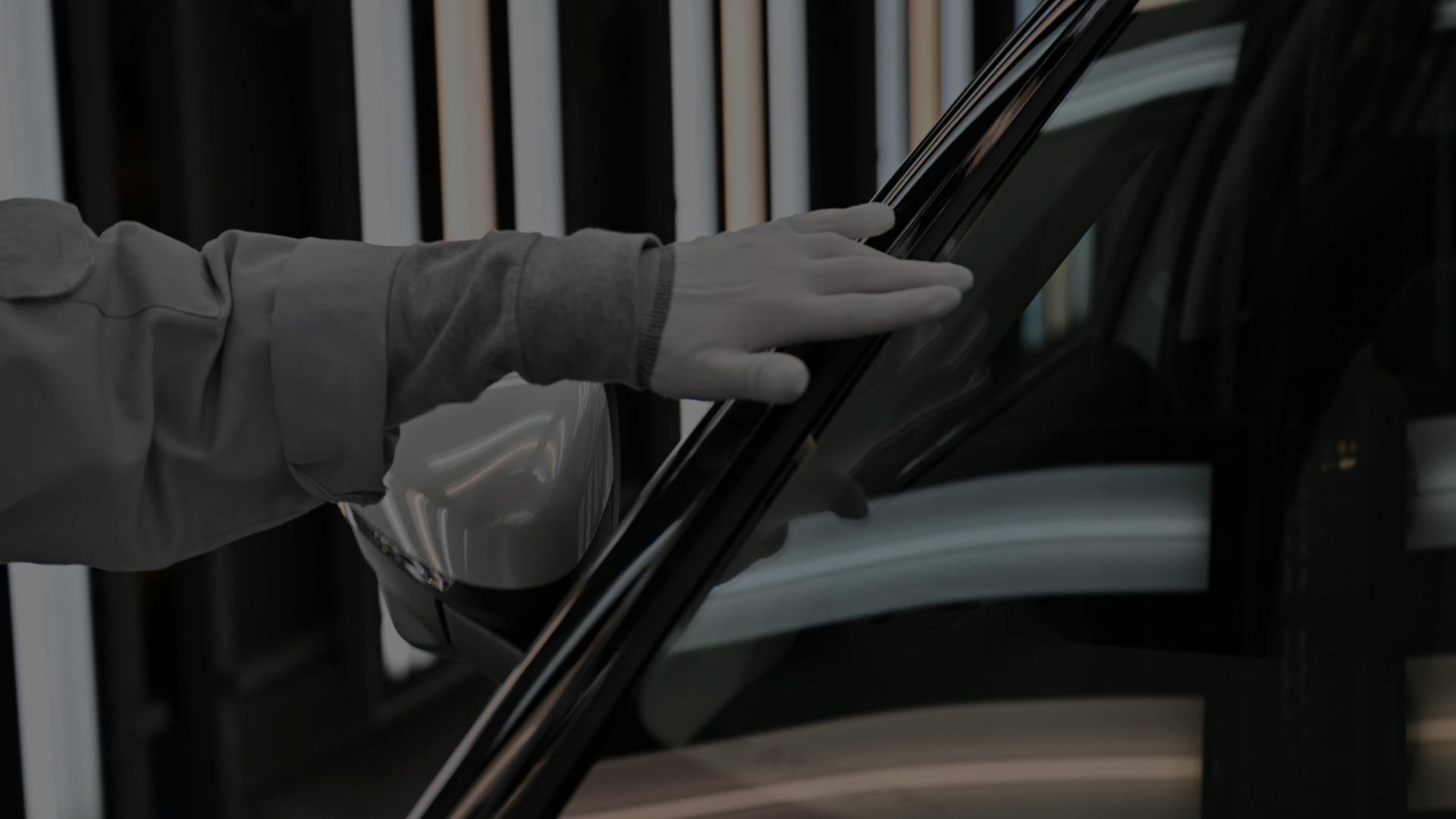
The following quality control areas are involved in the manufacturing process:
Destructive inspection: here the quality of welded connections, sealants and other body parameters are checked by destroying them with a special tool. The destructive inspection is necessary to confirm the quality of welding and to ensure that we produce vehicles with a high level of quality and safety.
Metrology: 3D body measurements, measurements of individual vehicle parts (on request), measurements of clearances between closures (doors, bonnet, boot) and the body.
Chemical laboratory: chemical analysis of plastic parts and paintwork.
Destructive inspection: here the quality of welded connections, sealants and other body parameters are checked by destroying them with a special tool. The destructive inspection is necessary to confirm the quality of welding and to ensure that we produce vehicles with a high level of quality and safety.
Metrology: 3D body measurements, measurements of individual vehicle parts (on request), measurements of clearances between closures (doors, bonnet, boot) and the body.
Chemical laboratory: chemical analysis of plastic parts and paintwork.
“Quality Gates” are located in the workshops near the areas where the risk of defects is high.
“Light tunnel” is located at the end of the assembly line. Here the clearances are visually checked, defects and deformations are detected, opening and closing of doors and boot is checked. Defects are labelled with stickers and entered into an electronic database.
“Wheel alignment": alignment of wheels, adjustment of headlight flux.
“Underbody inspection” (inspection pit).
“Serial shower” (checking the leakproofness of the vehicle).
Vehicle electronics check point (installed programmes are read).
Test drive of the vehicle on a small or large test track: detection of noises, non-stop driving on paving stones, gravel surface, as well as over an overpass, rails, acoustic tunnel and emergency braking tunnel.
High quality, vehicle safety and ultimate customer-orientation in the production, sale and further maintenance of the vehicles are the absolute priorities of the company “Automotive technologies”!
“Light tunnel” is located at the end of the assembly line. Here the clearances are visually checked, defects and deformations are detected, opening and closing of doors and boot is checked. Defects are labelled with stickers and entered into an electronic database.
“Wheel alignment": alignment of wheels, adjustment of headlight flux.
“Dynamic engine test bench”: inspection of brake and steering systems at speeds up to 130 km/h.
“Underbody inspection” (inspection pit).
“Serial shower” (checking the leakproofness of the vehicle).
Vehicle electronics check point (installed programmes are read).
Test drive of the vehicle on a small or large test track: detection of noises, non-stop driving on paving stones, gravel surface, as well as over an overpass, rails, acoustic tunnel and emergency braking tunnel.
High quality, vehicle safety and ultimate customer-orientation in the production, sale and further maintenance of the vehicles are the absolute priorities of the company “Automotive technologies”!
PHOTO AND VIDEO
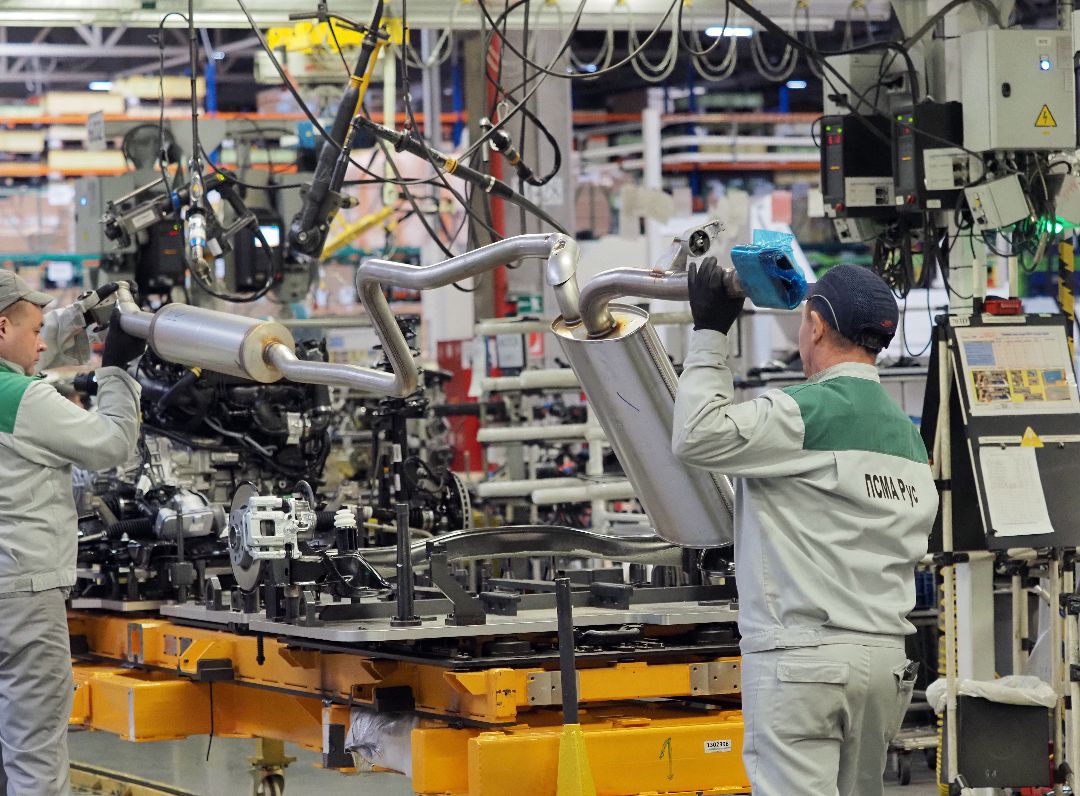
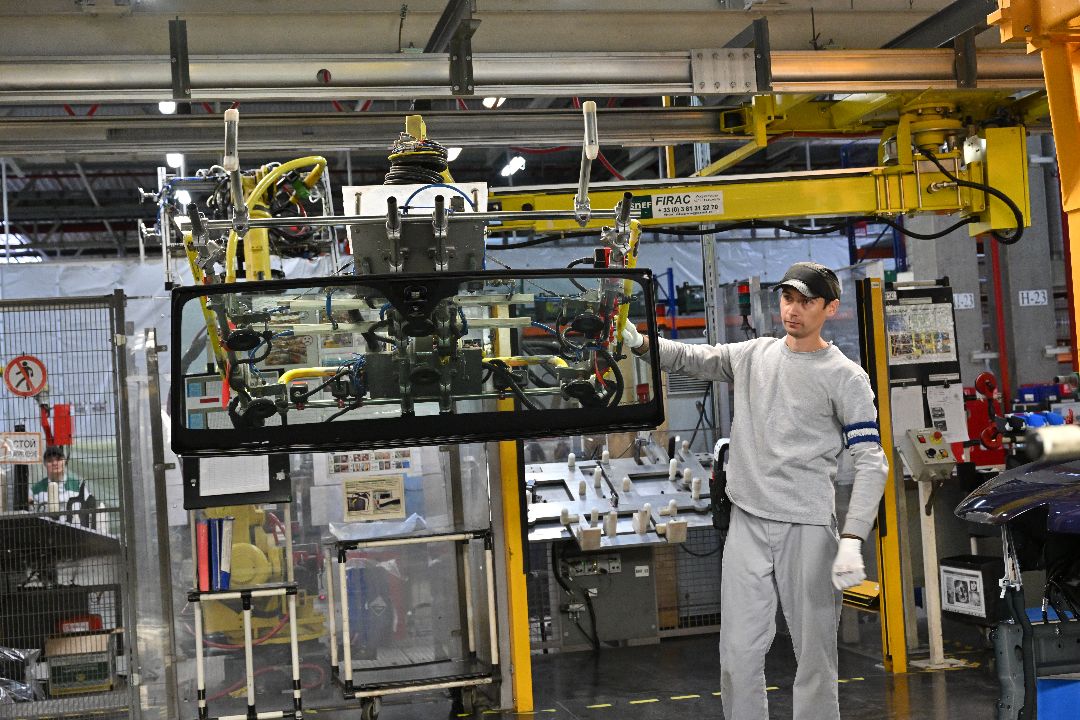
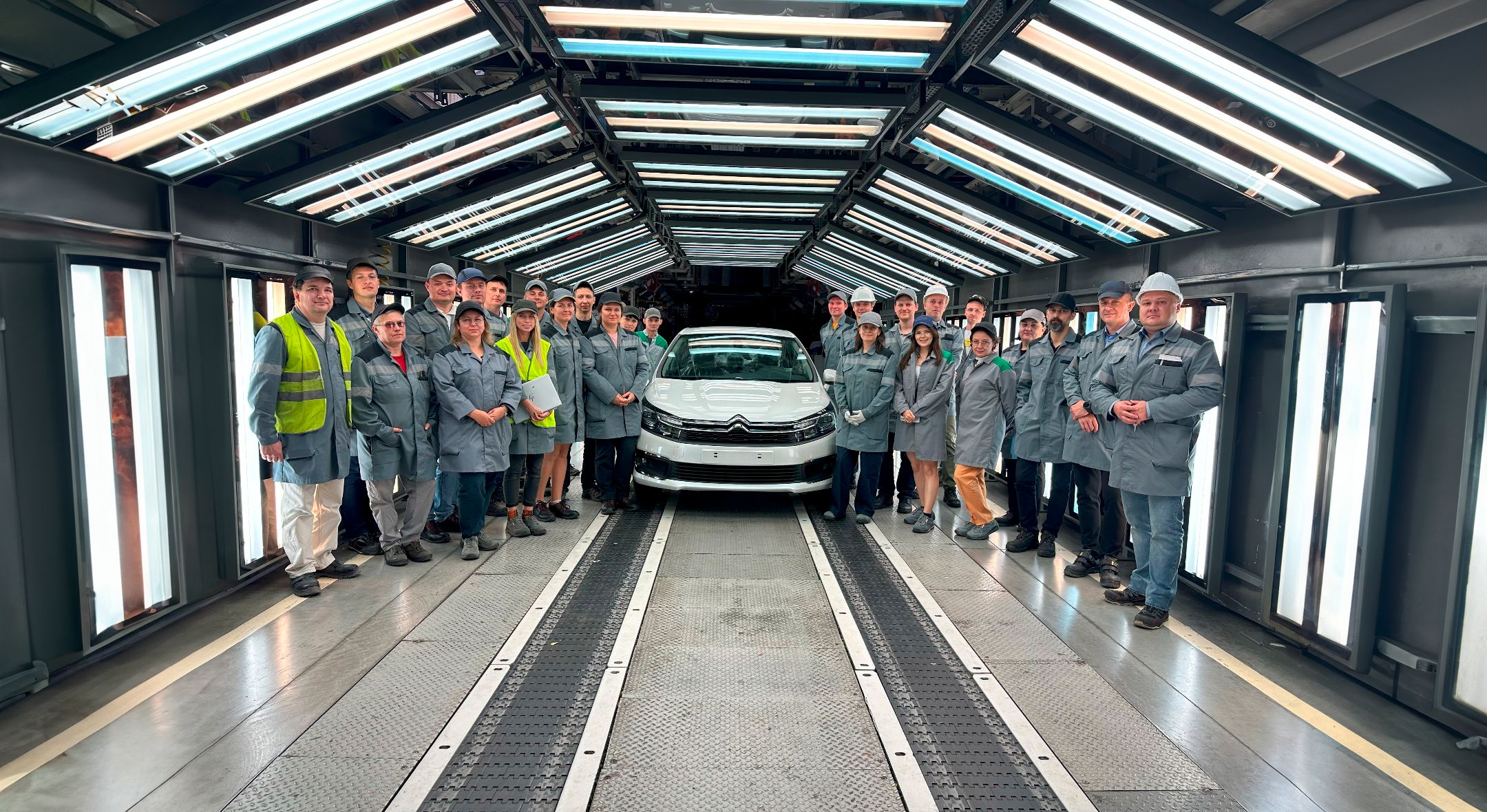
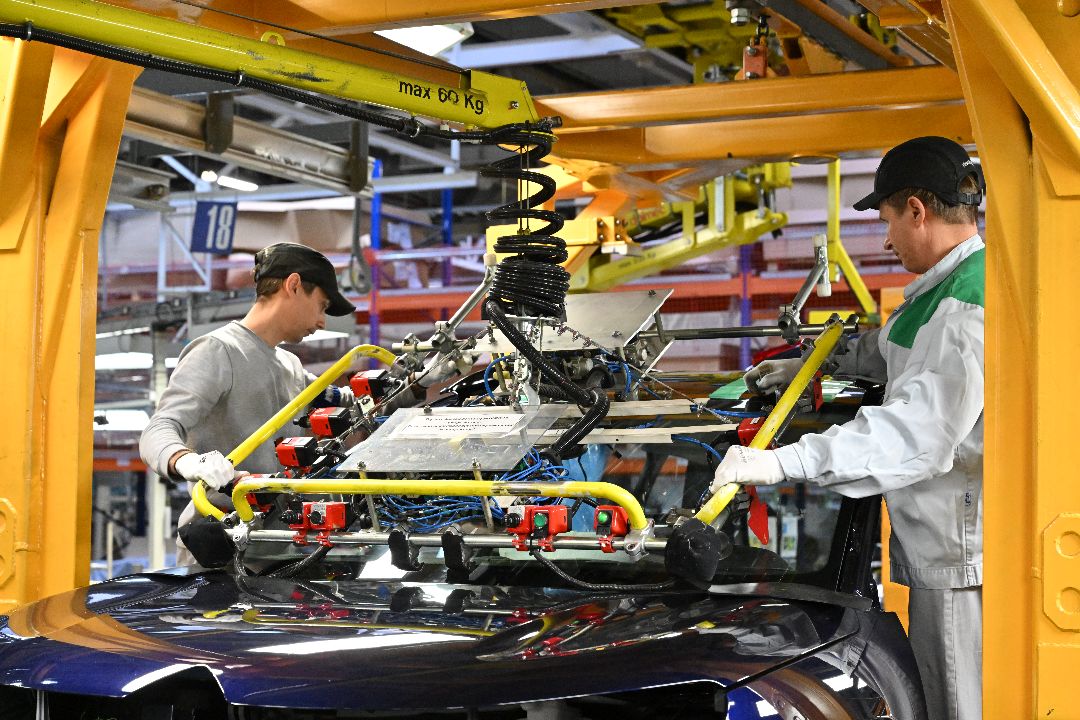
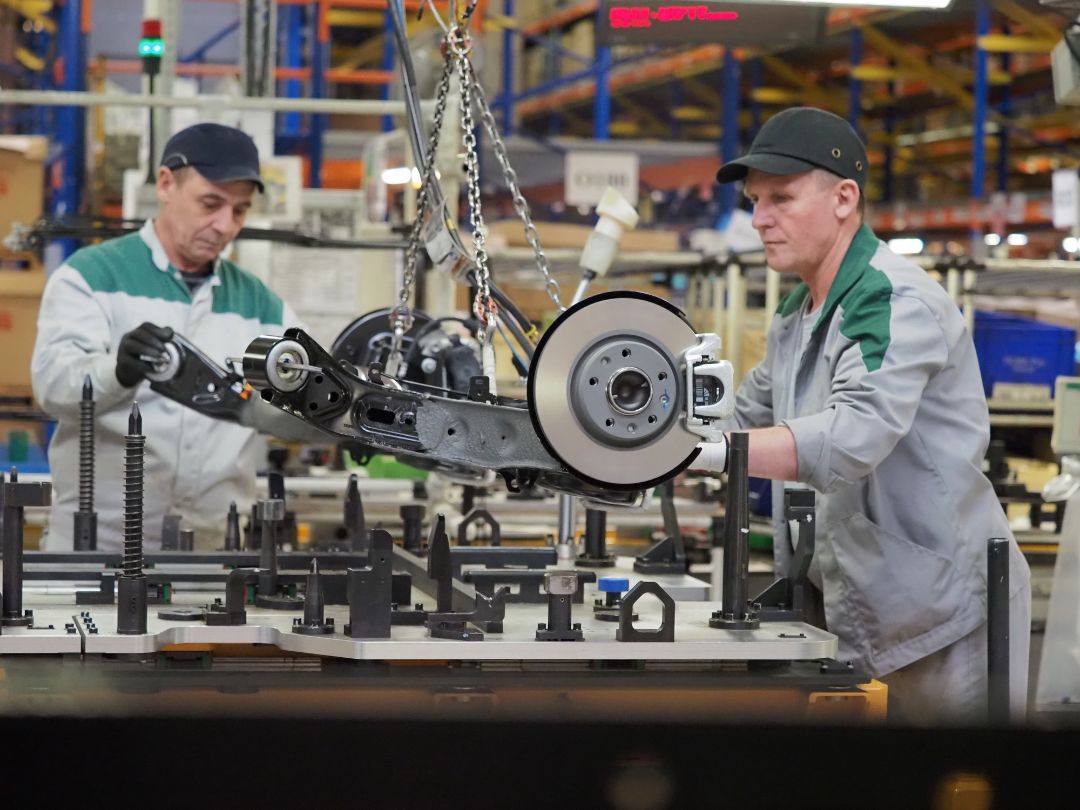
REQUIREMENTS AND PROCEDURES FOR SELECTED SUPPLIERS
This section contains requirements and procedures that are mandatory for all suppliers who make serial deliveries of parts/materials to the “Automotive technologies” plant.